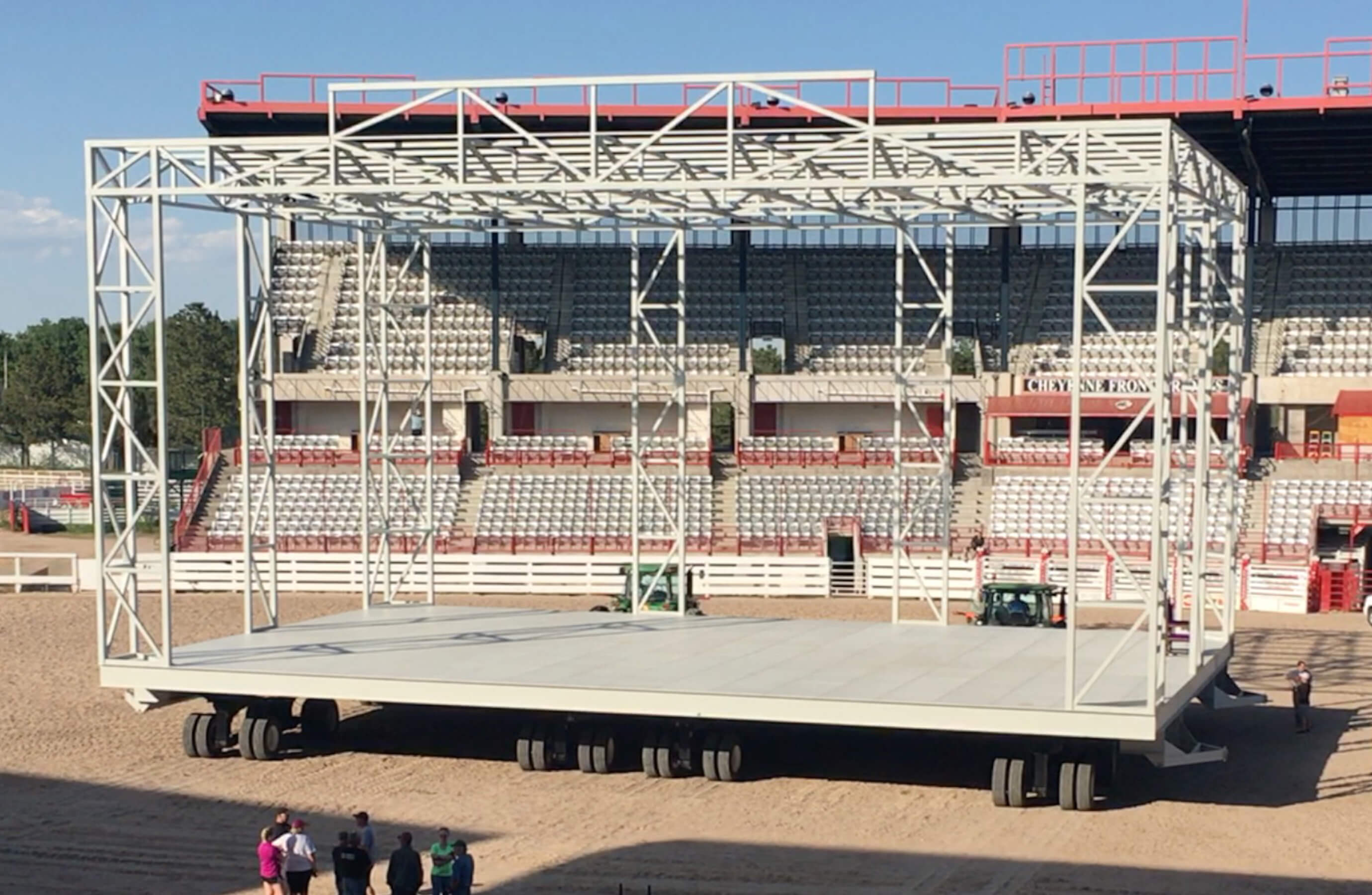
Project – Stage Moving
HMR Supplies recently completed a large project in Wyoming. The challenge, to design a system to move a 50′ X 80′, 200,000 LB outdoor performance stage 200 yards. The customer requested a moving system be attached under the stage so that it could be move into an exact position between shows at the Cheyenne Frontier Days venue. Customer specifications indicated a 20 minute time requirement to move the stage into place and that the power to move the stage be provided by a two tractors. HMR Supplies designed a system using six custom dollies to move the stage.
Project engineering, specification drawings, programming, weight performance testing were completed at HMR Supplies facilities in Iowa.
To complete the project, HMR Supplies manufactured 6 dollies with a knuckle suspension. Steering and height were controlled by a hand held remote attached by umbilical cord and powered by a Holland Power Unit.
-The knuckle suspension on the dollies was 67.16 inches tall when collapsed and 85.66 inches tall when fully extended provided a lift of 18 inches. The knuckle suspension also provided a 135 degree turning capability to the stage.
-Each dolly weighed 10,000 LBS with a 56 inch wheel track, and eight 315/80R 22.4 20 ply tires.
-Spring applied brakes on the four outside modules for parking.
-The 100 hp. power unit featured a Fiat Power train diesel engine, a 30ft umbilical to the remote, 3 lifting zones, 2 steering zones, and 2 braking zones, and on board air compressor.
The project was installed and tested in June 2016. Testing onsite was successful, meeting customer requirements.
The project highlighted the work that we do best, customizing the Holland Dollie®product to meet the needs of the customer’s project.
Video of the project test footage and installation can be viewed here: https://youtu.be/NmxM4O5C8Ig
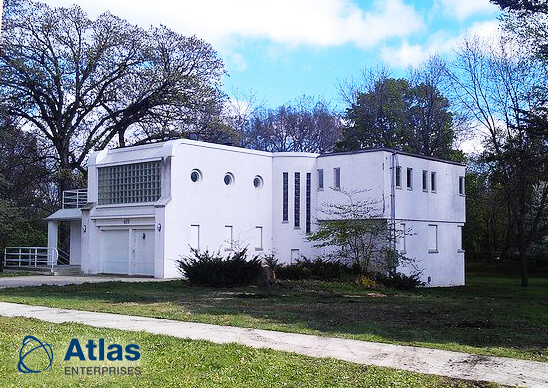
Egloff House Move
copy
Holland Corporations manufacture a bridge to complete historical Egloff House Move in Mason City, Iowa
Forest City – Built in 1938, the Historic Egloff house on 7thStreet NE in Mason City was damaged by flooding in 2008. The home is considered an outstanding example of the International Style of Architecture. City officials and historic preservationist joined to create the non-profit, Community Benefit – Mason City who worked hard to raise funds to save the home from demolition. Atlas Enterprises, one of three companies of the Holland Corporations was hired by the Community Benefit Group to move the home and several nearby structures to higher ground on State Street in Mason City.
Project discussions began in 2013, with several of the smaller nearby homes moved in Fall and Winter of 2014. The route to move the homes brought the Egloff house over the 100 year old North Carolina Bridge. The Egloff home is a concrete structure that exceeded 400,000 pounds and project engineers determined that the weight of the home exceeded the limitations of the bridge. HMR Supplies, another of the Holland Corporations, engineered and manufactured a bridge that was placed over the North Carolina Bridge to distribute the load of the home off the bridge as it crossed over.
“The challenge of engineering and manufacturing a bridge is what makes this project unique for us” says President, Chris Holland. “The bridge showcased our engineering and manufacturing capabilities. We accepted the challenge are pleased with the results”.
The bridge took several months to design and manufacture at the HMR Supplies facility in Forest City. The temporary bridge was constructed of four steel platforms that were connected by a bolster in the center of the bridge. The length was 136 feet, the width 29 feet and the weight was just over 260 thousand pounds. Over 1500 heavy hex bolts were used to construct the four steel platform bridge sections. The bridge sections were transported by truck to the North Carolina Bridge. Assembly of the bridge on site took four days. (See attachment 1).
The Egloff House move took place on August 24th, 2015. It took approximately 45 minutes to cross the temporary bridge. A structural moving crew of ten were constantly observing the structure, dollies, utility lines, trees and the amount of displacement on the temporary bridge as the historical home inched its way over the bridge toward its destination on State Street. The Egloff House was fitted with 10 Holland Dollies, two power dollies in the front and back of the structure, which propelled and steered the home using remote controlled devices. The other 8 dollies were coaster dollies. Following close behind the Egloff House was its garage section. The sheer size and weight of the house and garage necessitated that they be cut apart and moved separately.
copy
cipy
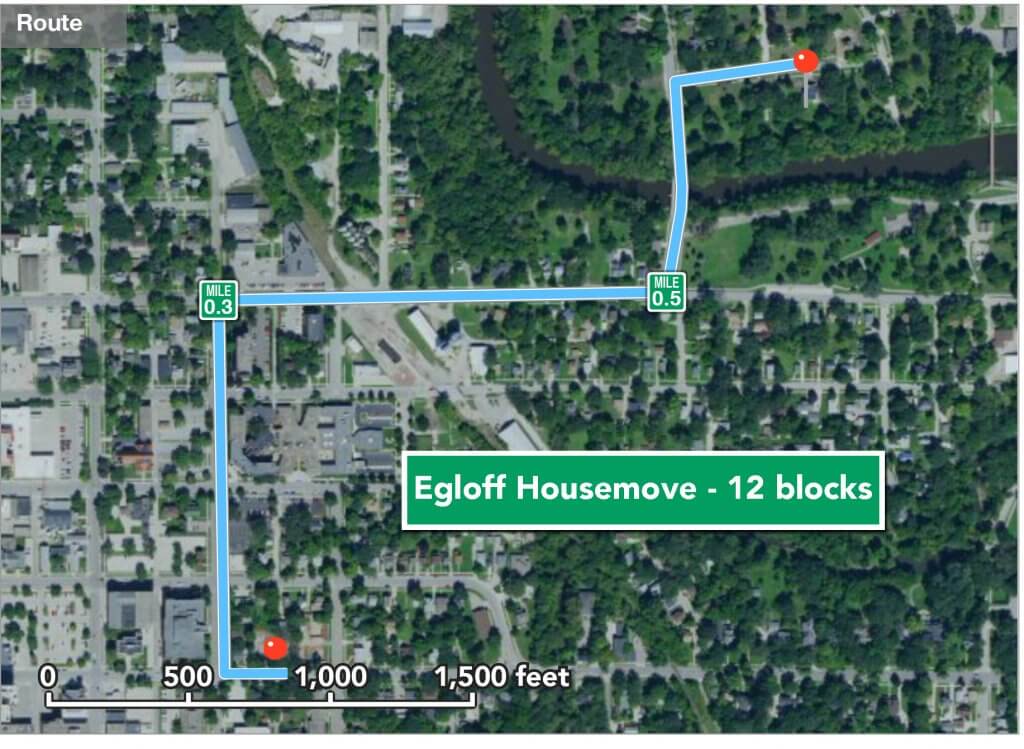
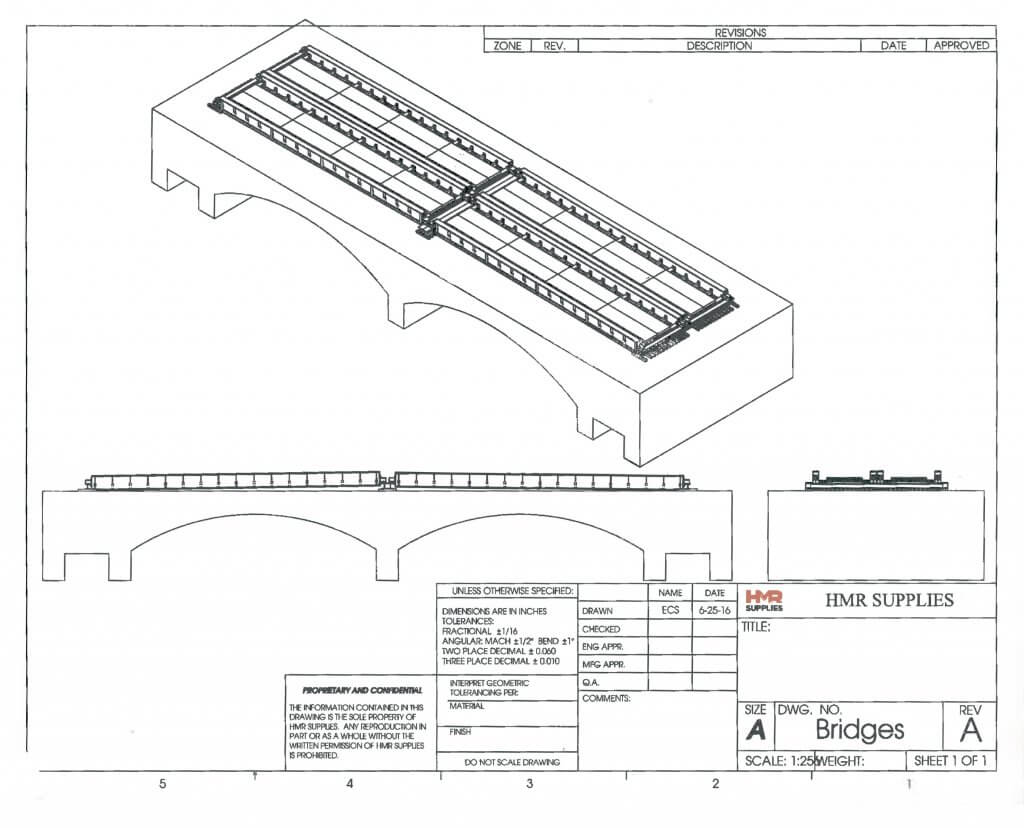
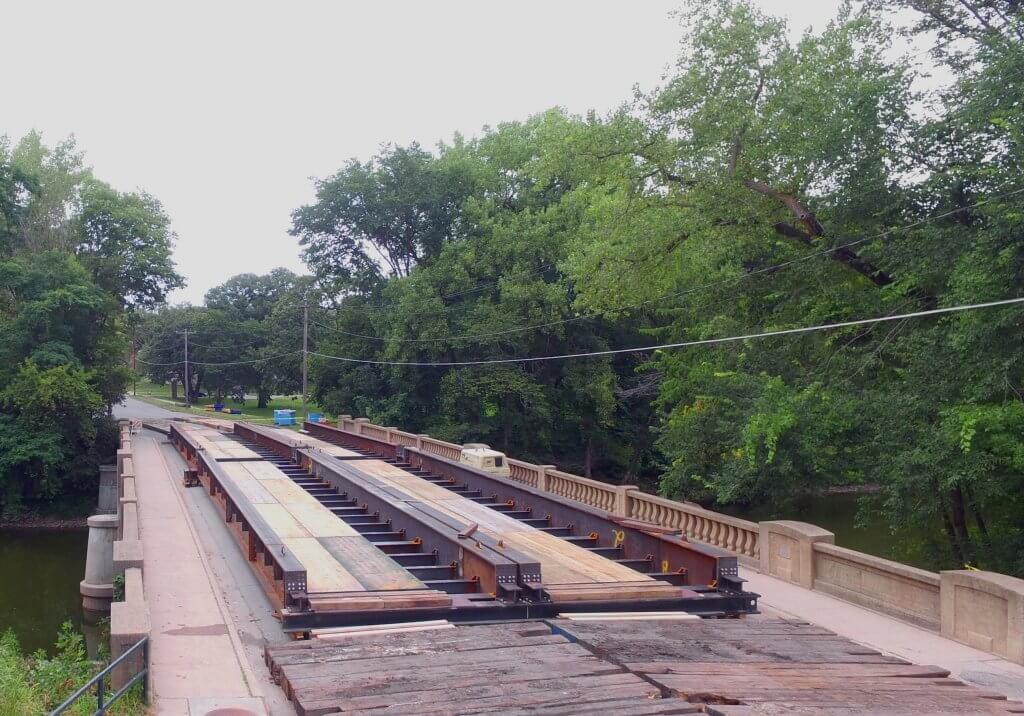
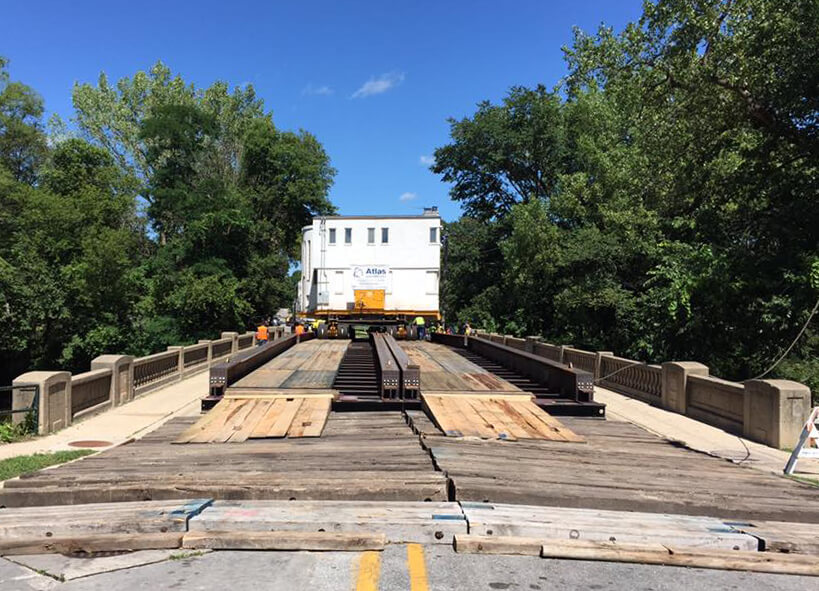
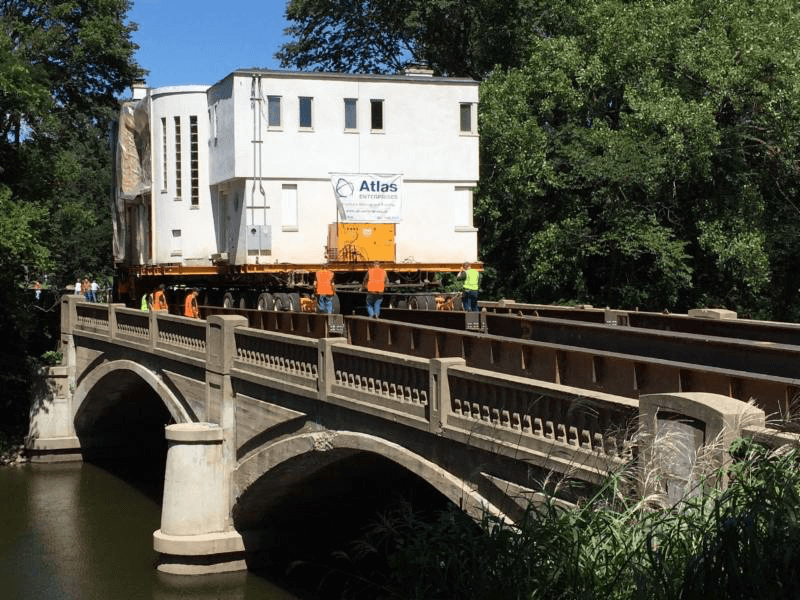
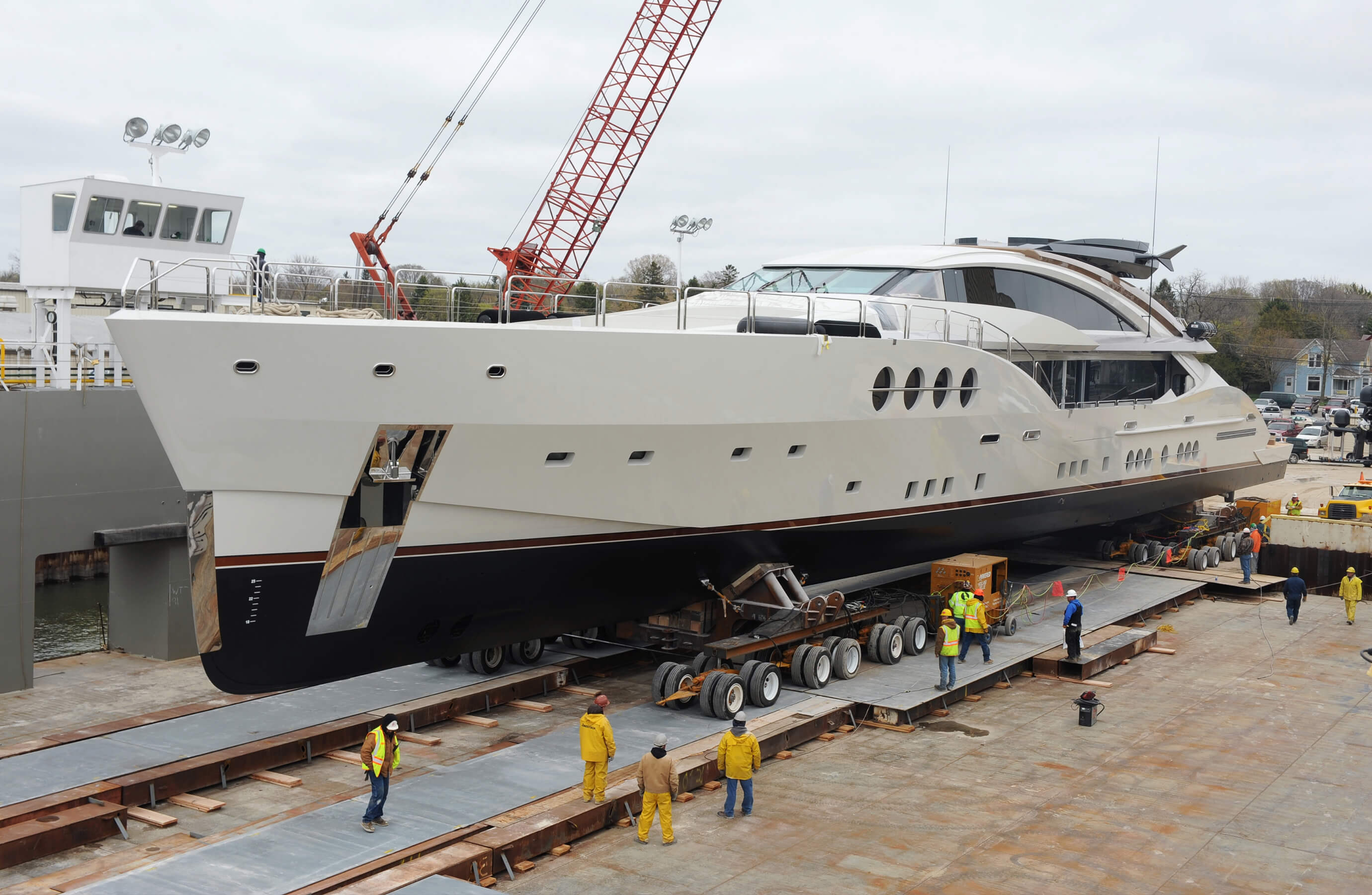
Yacht Move
HMR Supplies and sister companies Atlas Enterprises, a structural moving company, and CR Holland Crane Service worked together to complete a large yacht move in 2013. The superyacht was the heaviest object HMR Supplies employees have transported since it was founded as Ron Holland Housemoving in the early 70s. At 215-foot long, the 480-ton structure was equipped with a swimming pool on deck that doubled as a helicopter pad when the pool cover closed over the top.
“It’s not the largest thing I have ever driven,” said Chris Holland, president of HMR Supplies and Atlas Enterprises. “The company also needed the skilled engineering and professional experience of the Atlas team to get the superyacht, which is long enough and heavy enough to be classified as an ocean liner, to the body of water it uses for its sea trails. Due to the size of the superyacht, there was very little room in the fabrication facility for placement of trailers under the yacht.
“The small footprint of our modular Holland Dollies made the move possible,” said Holland.
The move began with two full days of preparation that included completing the bolster and cradle system that had been engineered and fabricated by HMR Supplies. Once the yacht was securely nestled into the bolster system, the dollies that ultimately carried the superyacht onto the barge were put into position. The move ended after an 8-hour session that required the removal of the doorway header within the fabrication facility due to only three inches of clearance for height and navigation of a 90-degree turn in tight quarters.
“It was highly satisfying to see it all work smoothly,” said Holland. “Several times the margin of error was as low as two inches. I’m incredibly proud of our team,” he said.
Project equipment included 12 Coaster Holland Dollies, 4 Powered Holland Dollies and 2 power units. No push or pull truck was used to move the yacht. Holland said two power dollies placed in front propelled the superyacht out of the fabrication building and through the city streets. To reach the launch area, the structure had to navigate an extremely tight fit between a building and a fence just before making the 90-degree turn.